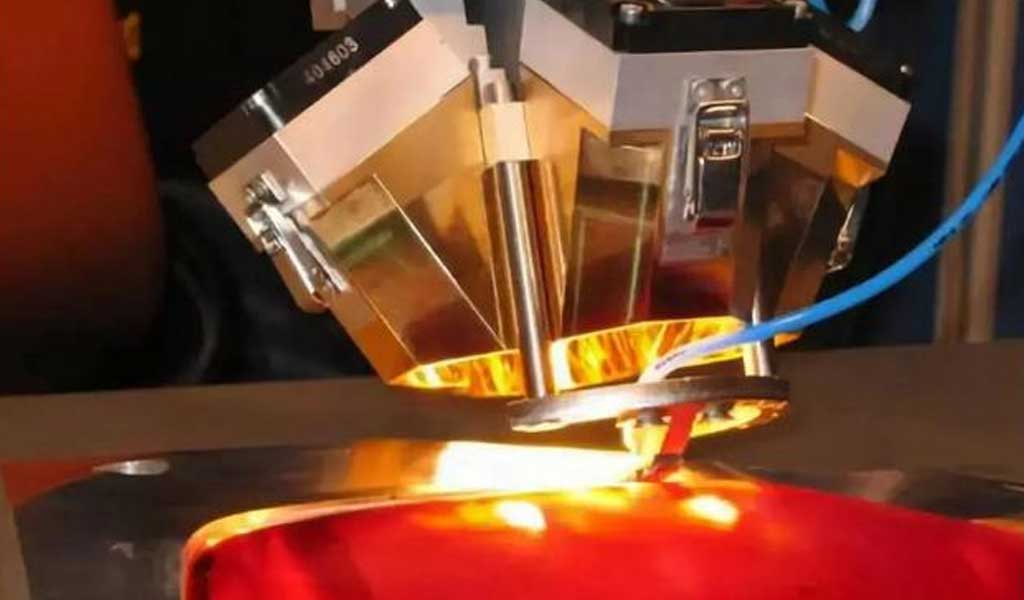
Laser welding occupies an important position in the field of material processing. Traditional laser welding is mainly carried out between metal materials. However, with the development and progress of technology, laser welding between dissimilar materials has also become an important breakthrough direction. This paper mainly studies metal Laser welding technology with plastics.
Plastic is actually a kind of polymer. The principle of laser directly connecting metal and polymer is mainly to generate high temperature through laser irradiation of metal and reach the polymer through thermal conduction, generate a melting area near the connecting interface of the polymer, and excite tiny particles inside it. Bubbles, the generation of bubbles or rapid expansion produce high internal pressure that makes the molten polymer stick closely to the surface of the metal, while pushing the molten polymer into the metal, because of its rough surface, the result is between the metal and the polymer. Create a physical connection (van der Waals forces), a mechanical connection (called the anchoring effect) or a chemical connection. The following introduces several key technologies in sheet metal welding from different angles.
Welding Materials
In 2007, S. Katayama of Osaka University and others first verified the feasibility of laser direct connection between metal and plastic by using YAG laser with SUS304 stainless steel and amorphous PA6 (polyamide 6) as materials. LAMP (Laser Assisted Metal to Plastic Welding) [1] was proposed once, and it has been proved that the welding of various metals and plastics is feasible. For example, SUS304 stainless steel and PET (polyethylene terephthalate), which can produce chemical bonds between metal-Cr-O-polymers, such as galvanized steel sheet and PAN (polyacrylonitrile) type)\CFRP (carbon fiber reinforced plastic), which can produce a bond between the alloy and the plastic. Jiangsu University in China also started the welding research of metal and plastic earlier. Xiao Wang et al. [2] used titanium and PET for welding, and found that Ti-C chemical bond was formed. In the research, a lower welding power was used. and increased clamping force.
The connection effect between different materials is also different. As far as polymer materials are concerned, the volume, number and size of bubbles formed by different polymer materials after receiving heat are different, which directly affects the welding area and welding strength. For example Yukio MIYASHITA et al. found that the weldable ranges of PET and PC and SUS stainless steel are different [3]. As far as metals are concerned, different metals have different laser absorption and thermal conductivity, which directly leads to the difference in the size of the welding area. , and also affects the failure loading force of metal welding. The Nagaoka University team used three different metals, namely copper, SUS304 stainless steel and A5052 alloy, to laser weld with PET under the same conditions. PET/SUS304 has the highest welding strength [4].
Laser
In the welding of metal and plastic, the choice of laser is particularly important. Different lasers produce different ways, beams and power ranges used. Currently, the following lasers are used:
Nd:YAG Laser
That is, yttrium aluminum garnet crystal, yttrium aluminum garnet crystal as its active material, belongs to solid laser, can excite pulse laser or continuous laser, the emitted laser is infrared wavelength of 1.064μm, and the generated light is monochromatic light.
Semiconductor Laser
Semiconductor lasers, also known as laser diodes, are lasers that use semiconductor materials as working substances. Commonly used working substances are gallium arsenide (GaAs), cadmium sulfide (CdS), indium phosphide (InP), zinc sulfide (ZnS), etc. There are three types of excitation methods: electric injection, electron beam excitation and optical pumping. That is, the semiconductor laser can realize two working modes: pulsed and continuous.
The YAG laser has a cone beam and the semiconductor laser can generate a linear beam. The irradiation from the plastic side can realize the welding of metal and plastic. Adjusting the focal length of the YAG laser can change the strength of the bonding. The semiconductor laser can greatly improve the bonding strength. A power continuous laser beam can produce deeper penetration, and Jiangsu University used a near-infrared diode laser to weld titanium and PET, and a weld area with a diameter of 900 μm was obtained [4].
Femtosecond Lasers
Femtosecond laser is an ultra-short pulse laser, which is not widely used in the field of metal welding at present. In 2013, Tomokazu Sano et al. also used a femtosecond laser to realize the welding of metal and plastic. The study also found that the distance between the pulses and the distance between the lines has a greater impact on the welding strength [5].
Welding Process Optimization
During the welding process, many process factors will affect the welding strength. Laser welding mainly depends on the input of heat, so heat plays a leading role in improving the welding strength. The main manifestations are: a. With the increase of power during welding, the tensile force will have a rising peak, and then it will drop at a certain point, and the same welding speed has a similar effect; b. The proportion of the joint increases, and the joint strength is also corresponding. Increase. The above research also proves that although the input of heat is the dominant factor, it is not that the greater the input heat, the better the welding effect, and there is a saturation point in the welding strength curve.
In addition, the method of laser irradiation also has an impact. At present, the method of laser irradiation from the side of the plastic is widely adopted, which can make the laser beam directly irradiate the assembly part, generate high heat instantly, and improve the strength of the connection.
In addition, there are other factors that affect welding. In 2011, Katayama Shengji et al. found that: a. Laser-induced feathering. Feathering will occur when the laser irradiates the metal, among which the high feather will cause shallow welding; b. Laser absorption. When the beam is smaller, the energy is higher, or the welding speed is lower, the light absorption will be higher, and a “keyhole” structure will appear when the laser is injected. Different size, this size affects the absorption of light, thus affecting the welding effect [6]. Studies by Yukio Miyashita and others found that the state of the bubbles will change due to the magnitude and frequency of the applied force. The application of a moderate static force can inhibit the expansion of the bubbles, which is beneficial to the improvement of the welding strength; the application of periodic contact force will make the bubbles flow rapidly. , which reduces the bubble density, and the welding strength is smaller than the static pressure [7]. Therefore, a new method is proposed to improve the welding strength by applying different forces.
Surface Pretreatment
A large number of experiments have proved that when metal and plastic are welded, the plastic will be decomposed or melted by heat. If the metal surface is rough or has a certain microstructure, this part of the flowing plastic will enter these rough parts of the metal, and after rapid cooling , the plastic will stay in these microstructures and produce an anchoring effect. Therefore, many researchers have begun to treat the metal surface, hoping to obtain an ideal surface microstructure and increase the strength of the welding. These treatments include physical, chemical and other means. Since there is usually an oxide layer on the metal surface, it may affect the connection between metal and plastic. Wahba M[9] and others took pretreatment measures before welding. First, the metal sample AZ91D was rubbed to remove the surface oxide layer, and then the surface oxide layer was removed. Cleaning with acetone followed by laser surface treatment of metal samples enhances the bond strength through such pretreatment. In addition, researchers have also developed methods such as using UV-ozone [10] for polymeric materials, with different pretreatment methods. The resulting holes are different, and deeper holes can of course be anchored deeper.
Conclusion
Extensive attempts have been made for laser welding of metals and plastics. In the future, we can focus on key materials used in aviation, biology and other fields. There is still a lot of room for experimentation in the selection of lasers and the optimization of welding processes, and integrated systems can be added. In order to form an industrialized mass production system; in addition to the traditional chemical and physical methods, the surface treatment can also give good ideas through the surface modification of materials at the molecular level. The further development of laser welding of metals and plastics is sure to bring surprising results in the emerging field of manufacturing.