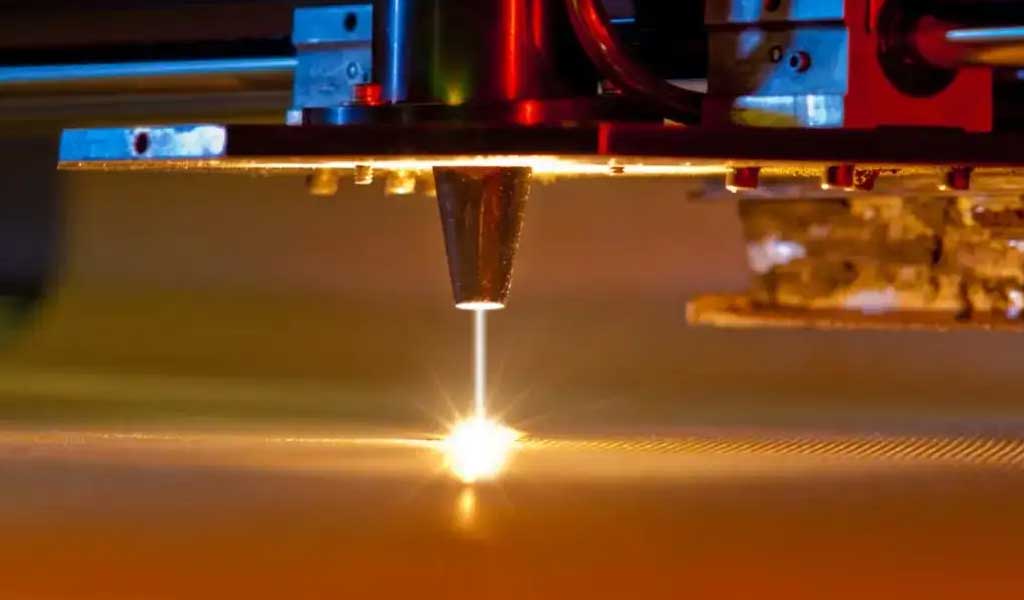
The technology of using laser high-energy beam to treat material surface is a new technology of material surface treatment developed rapidly in recent years. composition and structure to achieve surface modification of materials.
The characteristics of laser surface modification technology: high energy density of heat source, non-contact heating, small heat affected zone, small influence on the performance and size of the workpiece substrate, strong process controllability, environmental protection and other advantages. In recent years, with the further improvement of material surface performance requirements, new energy technology has been gradually improved, and the application field of laser surface modification technology has become wider and wider. However, compared with traditional surface surfacing and spraying, the cost of laser surface modification technology is higher, and the powder alloys and process parameters required to prepare surface alloy layers with different compositions are different. These parameters need to be further explored and studied, which also To a certain extent, it restricts the development of this technology.
Laser Surface Modification Technology And Application
Laser surface modification technology includes a variety of processes: laser quenching, laser surface alloying, laser surface cladding and laser rapid melting. At present, laser surface modification technology has been widely used in automobile manufacturing and processing, precision machinery manufacturing and processing industries.
2.1 Laser hardening
Laser quenching is the earliest laser processing technology applied to the surface strengthening of metal materials. Laser quenching is to rapidly irradiate the workpiece with a high-energy density laser beam, so that the surface temperature rises rapidly above AC3 (below the melting point) to form austenite. When the laser beam is removed, the workpiece is rapidly cooled by itself, forming a martensitic structure, realizing local transformation hardening of the material, and significantly improving the hardness and wear resistance of the metal material surface. Cai Lifang [3] and others used different laser powers to test ZL109 alloy. With the increase of laser power, the hardness increased by 40-100HV, and the wear resistance was increased by 1.6-2.2 times.
2.2 Laser surface alloying
Laser surface alloying is that under the action of high-energy beam laser, the external alloying elements and the metal surface are melted together, and then rapidly solidified on the surface of the substrate, and only in the melting zone and a small heat-affected zone. Changes in composition, structure and properties , the thermal influence on the substrate can be reduced to a minimum, and the deformation caused by it is also small. The melting depth is controlled by the irradiation time and the power of the laser, and an alloy layer with a depth of 0.02-2.0 mm can be formed on the surface of the base metal. Since the cooling rate is fast, the segregation is small, and the grain refining effect is remarkable. Thereby improving the wear resistance, corrosion resistance and oxidation resistance of the surface layer. Cai Lifang et al. used Si powder as the coating material and used a high-power CO2 laser for surface alloying treatment to prepare a high-silicon AL-Si alloy coating on the surface of the cast aluminum alloy. Cracks are metallurgically bonded to the matrix, and their hardness and wear resistance are significantly improved.
2.3 Laser surface cladding
Laser surface cladding means that the required alloy powder is melted by laser and then coated on the metal surface to form a metallurgical bond between the coating and the substrate. The cladding layer has low dilution but strong bonding force. Significantly improve the wear, corrosion, heat, oxidation and electrical properties of the surface of the base material. Different from laser surface alloying, the dilution of the matrix to the surface alloy is required to be the smallest, and the material with high hardness, wear resistance, heat resistance and corrosion resistance is usually selected as the cladding material. Kan Lina [4] et al. used Cr-Ni-Si alloy powder as raw material, and used laser cladding technology to prepare C13Ni5Si2-based metal silicide on the surface of titanium alloy, and tested the resistance of the coating under dry sliding wear conditions. The results show that the laser-clad Cr13Ni5Si2-based metal silicide is mainly composed of primary dendrites and a small amount of eutectic, and the coating has good wear resistance under dry sliding wear conditions.
2.4 Laser rapid melting
Laser rapid melting is to use a high power density laser to irradiate the metal surface in a very short time, so that the local area of the metal surface is heated to a higher temperature in an instant to melt it. Then, by means of the heat absorption and conduction of the liquid metal matrix, the melted surface metal is rapidly solidified. The obtained structure is the as-cast structure, which has higher hardness and better wear resistance. Ren Xudong [5] and others selected different coatings for laser rapid melting of QT700 crankshaft, and studied the changes of hardness and surface residual stress of QT700 crankshaft under the condition of rapid melting. The results show that the surface hardness and surface stress of the coatings are significantly improved during the laser rapid melting process. After rapid laser melting, a hardened layer with a thickness of 1.0 mm can be formed on the surface of the crankshaft specimen, and its maximum hardness can reach 588HV. When the laser pulse power was increased from 2.6GW/cm to 3.5GW/cm, the residual stress on the crankshaft surface increased from 316MPa to 490MPa.
Application Prospects In Boiler And Pressure Vessel Manufacturing
The gasifier is an important equipment in the coal chemical industry, and its main function is to convert pulverized coal into syngas. The working environment of the gasifier is high in temperature, and the medium is corrosive, oxidizing and scouring. Therefore, the inner surface of the gasifier is required to have high temperature oxidation resistance, corrosion resistance and erosion resistance. At present, the inner surface of the gasifier generally adopts the surfacing process, and a layer of high-temperature oxidation-resistant, corrosion-resistant and erosion-resistant alloys is surfacing. However, the processing efficiency is low, the process control is unstable, and the thickness of the surfacing layer formed is uneven. If laser surface cladding or laser surface alloying is used to prepare an alloy layer with high temperature oxidation resistance, corrosion resistance and erosion resistance on the gasifier substrate, the process controllability is strong, the dilution of the substrate to the surface alloy is very small, and the alloy layer is The performance is stable, the thickness is uniform and the processing efficiency is high, which greatly improves the safety and performance of the equipment.
The water wall is the main heating part of the power station boiler, which is distributed around the furnace. Its interior is flowing water or steam, and the exterior receives the radiation of the boiler furnace flame and the erosion and wear of pulverized coal particles. The outer wall of the water cooling wall usually adopts the spray alloy process. During the operation of the boiler, the surface coating of the water wall often peels off. Laser surface cladding or laser surface alloying can be used to prepare a metallurgical bonding layer with high temperature resistance and erosion resistance on the outer surface of the water cooling wall, which can reduce the bursting phenomenon of the water cooling wall and greatly improve the service life of the water cooling wall.
Conclusion
Using laser surface modification technology, alloy layers can be prepared on the surface of some metals with low price and poor surface properties, which can be used to replace expensive metals, save precious metal materials, and make common materials obtain greater application value, thereby greatly reducing costs. The laser surface modification technology has no pollution and has almost no negative effects on environmental protection. The obvious performance advantages will make the laser surface modification technology have broader application and development prospects.