In the realm of precision engineering and micro-manufacturing, the advent of laser technology has revolutionized the landscape, particularly in micro laser cutting. The ability to fabricate intricate designs and achieve precision at a micro-scale has opened avenues across industries, from electronics and medical devices to aerospace and automotive sectors. A key aspect enabling this innovation lies in the diverse range of materials that can be effectively processed through micro laser cutting techniques. This article delves into an expansive exploration of materials utilized in this cutting-edge technology.
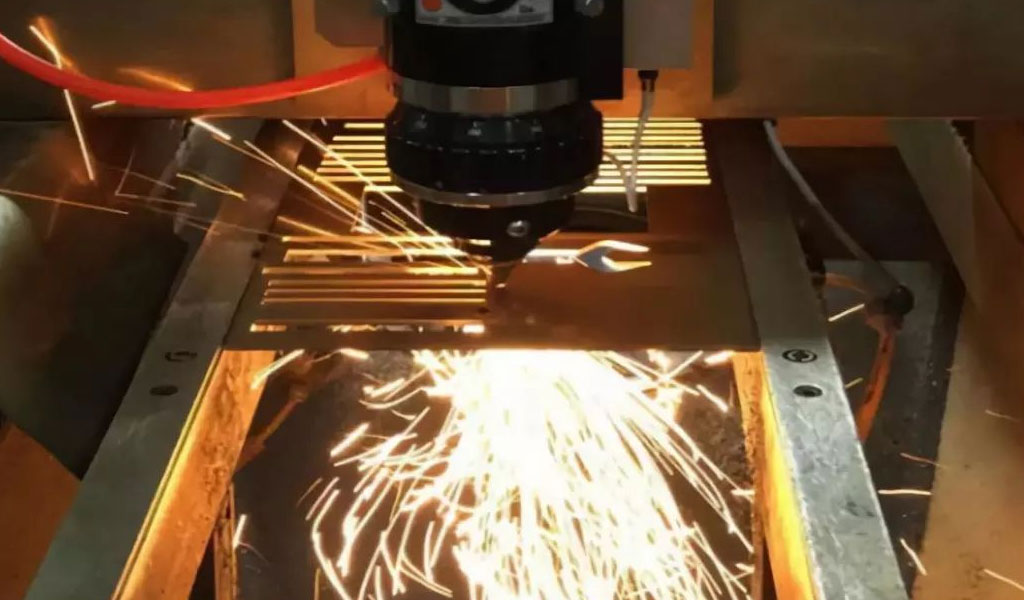
Understanding Micro Laser Cutting
Micro laser cutting is a high-precision process that involves using a focused laser beam to cut, engrave, or etch materials at a miniature scale. This technology utilizes various types of lasers such as CO2, fiber, and ultrashort pulse lasers, each catering to specific material properties and cutting requirements. The intricate nature of this technique allows for precise and intricate designs on materials that might otherwise prove challenging or impossible with conventional cutting methods.
Materials and Their Properties
Metals
- 1. Stainless Steel: Renowned for its corrosion resistance and durability, stainless steel is a common material in micro laser cutting applications. Its ability to withstand high temperatures without deformation makes it suitable for intricate designs in industries like medical devices, electronics, and automotive parts.
- 2. Aluminum: Lightweight and malleable, aluminum is widely used in micro laser cutting due to its conductivity and reflectivity. It finds applications in aerospace components, electronics housings, and intricate designs due to its ease of manipulation under laser processing.
- 3. Titanium: Known for its high strength-to-weight ratio and corrosion resistance, titanium presents challenges in machining due to its hardness. Micro laser cutting techniques allow for precise shaping of titanium, making it useful in medical implants, aerospace parts, and high-performance engineering components.
Polymers
- 1. Acrylic (PMMA): Acrylic is a transparent thermoplastic known for its optical clarity and UV resistance. Micro laser cutting acrylic enables intricate designs for signage, displays, medical devices, and even artistic creations due to its ease of processing and adaptability to various laser wavelengths.
- 2. Polycarbonate: Offering exceptional impact resistance and optical clarity, polycarbonate is a versatile material in micro laser cutting. It finds applications in protective equipment, electronic components, and automotive parts where durability and transparency are crucial.
- 3. Polyimide (Kapton): With excellent thermal stability and electrical insulation properties, polyimide is commonly used in electronics, particularly in flexible circuitry and electronic devices. Micro laser cutting allows for precise patterning and cutting of polyimide films for intricate circuit designs.
Ceramics
- 1. Silicon: Silicon, a semiconductor material, is extensively used in microelectronics. Laser cutting techniques facilitate precise shaping and etching of silicon wafers for semiconductor devices, sensors, and microelectromechanical systems (MEMS).
- 2. Alumina: Renowned for its high hardness, electrical insulation, and thermal resistance, alumina ceramics find applications in micro laser cutting for components in electronics, medical devices, and aerospace, where precise and durable materials are required.
Challenges and Innovations
While micro laser cutting has revolutionized manufacturing processes, challenges persist. Certain materials, like reflective metals, pose difficulties due to the reflection of laser energy. Innovations such as adaptive optics and specialized coatings have been developed to mitigate these challenges, enabling more effective processing of a broader range of materials.
Conclusion
Micro laser cutting continues to evolve as a pivotal technology in various industries, enabling the fabrication of intricate designs and precise components at a micro-scale. The diverse range of materials that can be effectively processed using this technique is expanding, propelling advancements in fields like electronics, medicine, aerospace, and beyond. With ongoing innovations and a deeper understanding of material properties, the potential applications and capabilities of micro laser cutting are boundless, promising a future of intricate, precise, and efficient manufacturing processes.