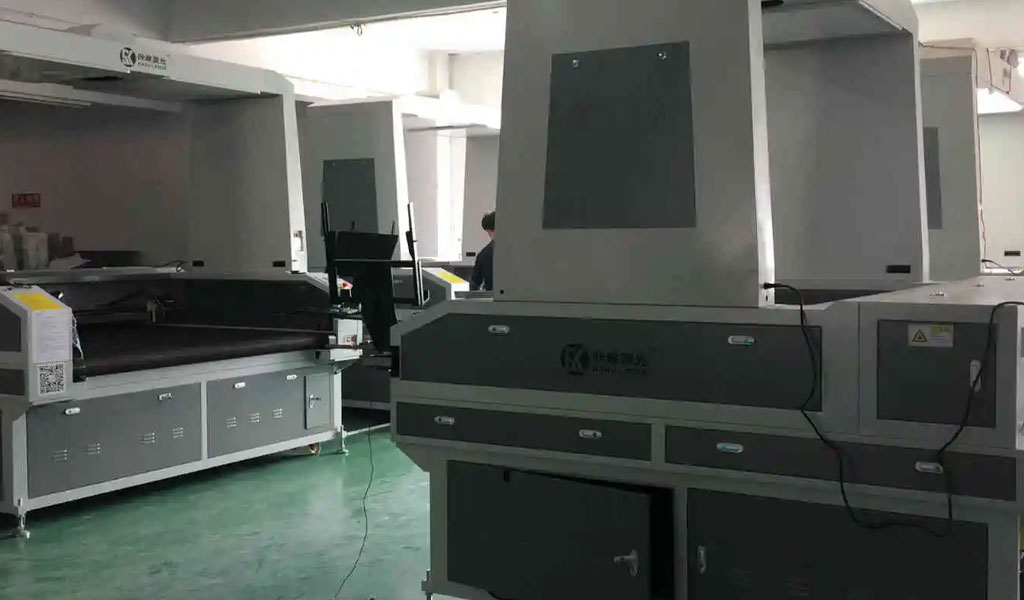
Today’s sheet metal enterprises, the use of laser cutting has long been commonplace. The advantage of laser cutting is that it is a fabrication method that does not touch the material, so it will not damage the surface of the sheet and leave no burrs on the cut surface. It is a fabrication method that can greatly reduce the subsequent processes. However, there are also various practical problems that are difficult to overcome in china laser cutting art. Here we will focus on the cutting difficulties and solutions of galvanized steel sheets that are commonly used in daily fabrication.
As we all know, the function of galvanized steel plate is to protect the carbon steel inside by galvanizing the surface, and it is a kind of plate that is not easy to rust after long-term use. Although this kind of plate is slightly more expensive than ordinary carbon steel plate, it is still cost-effective in terms of the cost of the entire product because it does not require subsequent processes such as spraying for rust prevention.
But after laser fabrication, the situation is different. From the perspective of auxiliary gas, there are generally three cutting processes for galvanized steel, namely air cutting, oxygen cutting and nitrogen cutting. Let’s first analyze the advantages and disadvantages of these three cutting processes:
Air cutting: The advantage is that the fabrication cost is extremely low, only the electricity costs of the laser itself and the air compressor need to be considered, and there is no need to generate high auxiliary gas costs, and the cutting efficiency on thin plates can match that of nitrogen cutting, which is an economical method. and efficient cutting method. But the shortcomings on the cut surface are equally obvious. First of all, the air-cut section will produce burrs on the bottom surface, and the products after laser fabrication must also undergo secondary fabrication such as deburring, which is not conducive to the entire product production cycle. Secondly, the air-cut section is prone to blackening, which affects the quality of the product. Therefore, the advantages of laser fabrication without subsequent fabrication cannot be reflected, so many companies are reluctant to choose the air cutting method in the fabrication of galvanized steel sheets.
Oxygen cutting: This is the most traditional and standard cutting method. The advantage is that the gas cost is low, and in the sheet metal fabrication mainly made of carbon steel, there is no need to switch the auxiliary gas frequently, which is convenient for factory management. But the disadvantage is that after oxygen cutting, a layer of oxide scale will remain on the surface of the cut surface. If this product with oxide scale is directly welded, the oxide scale will naturally peel off over time. This is one of the reasons why galvanized sheet welding is prone to virtual welding.
Nitrogen cutting: Nitrogen is used for high-speed fabrication. Since the role of nitrogen is different from the oxygen used for combustion, it plays a protective role, so the cutting section will not produce oxide skin. Many companies take advantage of this advantage, so the cutting of galvanized steel sheets is often processed with nitrogen. But the disadvantage of nitrogen cutting is here: because the cutting section is completely unprotected, the product is prone to rust. In order to prevent the product from rusting, it had to be sprayed again. As a result, the galvanized sheet that was bought at a higher cost did not have the characteristics of its galvanized layer, which is a pity.
Summarizing the advantages and disadvantages of the above fabrication methods, we recommend BE-CU’s unique solution for galvanized steel cutting, which is the super EZ cutting “HP EZ-CUTⅡ” fabrication technology. The so-called super EZ cutting means that the optional super EZ cutting device (which can be retrofitted) next to the standard model can solve all the above difficulties at one time and achieve high-quality, waste-free cutting.
The principle of the device is to use a special filter element. The characteristic of this filter element is that the oxygen passing rate is much higher than that of nitrogen. After the compressed air is injected into the filter element, the oxygen is discharged to the outside of the outer membrane. As a result, the gas obtained from the outlet of the filter element is a gas filled with nitrogen.
The same auxiliary gas cost as air cutting is adopted, and the cost of auxiliary gas is almost negligible to achieve a cutting section between oxygen cutting and nitrogen cutting. Although there will be a small amount of oxide scale on the cutting section, it has been proved by practice that it will not affect the cutting section. post process. On the contrary, because of these oxide skins, the cutting section is protected and it is not easy to rust.
Compared with oxygen cutting, there is no need to consider the problem of sharp corner fabrication. Corner cutting can be carried out at the commanded speed. In addition, the cutting speed equivalent to nitrogen cutting can greatly improve the fabrication efficiency.
In terms of consumables, it is only necessary to replace the filter element once a year, and the most important gas separation membrane can be used continuously for 5-15 years depending on the usage, and the production cost will not be affected by the cost of consumables.
Taking into account the savings in gas costs and the savings in subsequent processes, it can be said that super EZ cutting is currently the best choice for laser sheet metal fabrication of galvanized steel. Using cheaper fabrication methods to obtain higher quality products is the consistent policy of BE-CU to provide solutions for customers. It hopes to provide higher added value for your products through various unique functions. It is the concrete embodiment of the business philosophy of BE-CU and customers’ common development”.