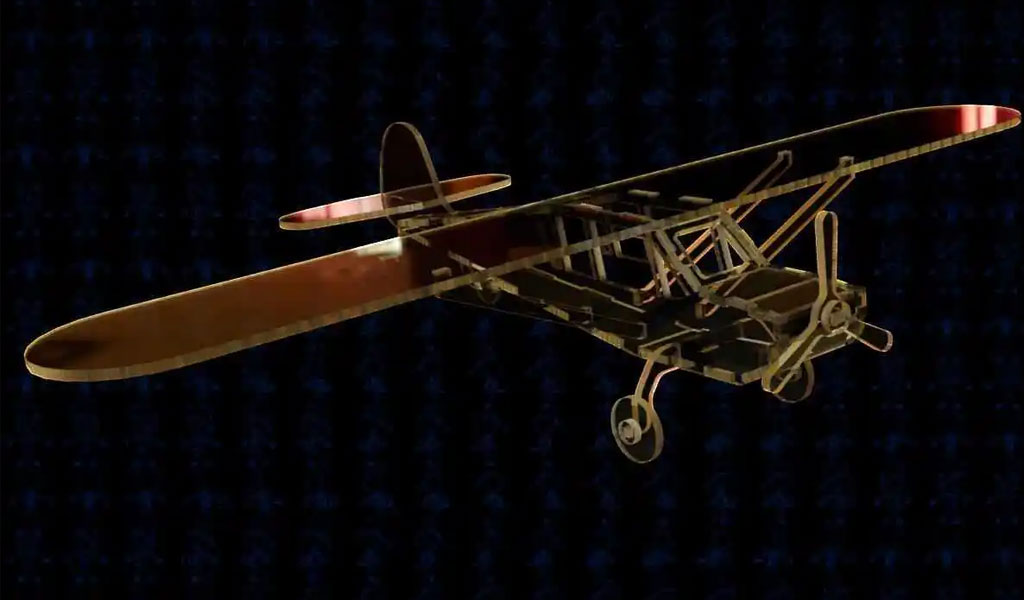
The use of welded integral fuselage panels instead of traditional riveted fuselage panels can greatly reduce the weight of components, reduce manufacturing costs, and improve production efficiency, so it has become one of the development trends of large-scale civil aircraft manufacturing technology. Because the double laser beam welding has a more obvious weight reduction effect on the skin truss structure, and has better spatial accessibility for complex components, it has received extensive attention. At present, aviation manufacturing companies such as Airbus have adopted the laser-welded integral fuselage panel manufacturing technology on their various models. However, the manufacturing technology of integral fuselage panel based on welding is one of the difficulties in the manufacturing technology of contemporary civil aircraft. At present, the new aluminum alloy welding technology of the fuselage wall plate in the design scheme of my country’s large passenger aircraft has its own characteristics in terms of manufacturability.
The Laser Weldability Overview Of Aluminum Alloys
Since the birth of the first laser welding machine in 1960, laser welding technology has developed rapidly [3]. In 1965, a ruby laser welding machine for thick film component welding was developed. In 1974, the world’s first five-axis laser fabrication machine, a gantry laser welding machine, was built at the Ford Motor Company. Later, the American Ford Motor Company developed a laser welding production line. Today, laser generators that can be used for welding have been developed from the first generation of CO2 gas lasers to YAG solid-state lasers, as well as the latest fiber lasers. The biggest advantage of laser welding is that its energy is concentrated, the aspect ratio of the welded joint is large, and the welding deformation is small. With the continuous improvement of laser beam quality, laser welding has now become a mature Industrial Welding method, which is widely used in different fields of national economy and national defense construction.
Aluminum alloy has low density, good corrosion resistance, high fatigue resistance, high specific strength and specific stiffness, and is an ideal material for aircraft structures. In recent years, although new materials such as titanium alloys and composite materials have received extensive attention in the aerospace industry, due to a series of advantages such as rich resources, excellent performance, easy fabrication, and low cost of aluminum, coupled with the new heat treatment state of traditional aluminum alloys With the development of new aluminum alloys (such as aluminum-lithium alloys), it is foreseeable that the application of aluminum alloys in aircraft structures will still have irreplaceable advantages for a long time in the future [4]. Therefore, aluminum alloy welding technology has become an important technical key. The use of laser welding technology to connect aluminum alloy aviation components has many advantages such as large welding seam aspect ratio, small welding heat affected zone, small welding deformation, and high welding speed. However, there are some technical difficulties in aluminum alloy laser welding.
- The aluminum alloy has a very high initial surface reflectivity to the laser beam (over 90% for CO2 laser, close to 80% for YAG laser), which requires a larger laser power before the formation of the molten pool [3] ;
- Due to the influence of multiple factors such as metallurgy and technology, the process of aluminum alloy laser welding is more likely to produce pores;
- Aluminum alloys are typical eutectic alloys, and hot cracks are more likely to occur under the condition of rapid solidification by laser welding;
- The adaptability of the laser welding gap is small, and the assembly accuracy of the weldment is relatively high;
- The coefficient of linear expansion of aluminum alloy is large, which is easy to produce welding deformation;
- The thermal conductivity of aluminum alloy is large, the cooling time is short, and the metallurgical reaction of the molten pool is insufficient, which is easy to cause defects;
- The liquid aluminum alloy has good fluidity, low surface tension and poor stability of the molten pool.
Despite the above difficulties, laser welding technology is still one of the most effective methods for aluminum alloy welding in the aerospace field. With the continuous testing and research, laser welding gradually showed its good process performance and mechanical properties after welding. Compared with traditional TIG welding and MIG welding, laser welding has the characteristics of high welding quality, high precision and fast speed. It is one of the fastest developing and most researched methods at present. In recent years, many international researchers have carried out a lot of research on aluminum alloy laser welding, and gradually formed a relatively reliable aluminum alloy laser welding technology.
Large Passenger Aircraft Fuselage Wall Panel Laser Welding Scheme
In the design scheme of my country’s large passenger aircraft, the laser welding process is initially considered in the manufacturing process of part of the lower wall panels of the front fuselage and the middle and rear fuselage. The position of the front fuselage welded panel is shown in Figure 1. Taking this panel as an example, the size of a single panel is 4276mm×1350mm, the thickness of the panel is 1.8mm, and there are as many as 9 stringers on a single panel, as shown in Figure 2. Therefore, it is a typical complex welding process with large size, small thickness and multiple welds.
In the above-mentioned fuselage skin stringer welding scheme, the dual laser beam bilateral synchronous welding process is mainly used. The double laser beam bilateral simultaneous welding of the T-connection structure of the skin stringer of the aircraft panel is a brand-new welding process. Because the T-shaped structure double-laser beam double-sided synchronous welding process avoids the damage to the integrity of the bottom plate (skin) by the traditional single-sided welding and double-sided forming process of the T-shaped structure, and this process can greatly improve the integrity of the bottom plate (skin) compared with the traditional riveting process. Reduce the weight of components, so it is favored in the aerospace industry. However, since the thickness of the panels and stringers is only 1.8mm, and the single panel has large dimensions in both the length and width directions, it is necessary to form multiple high-strength effective welds in this member, while controlling Insufficient welding, restraining welding deformation and stress concentration, the welded components must meet the indicators of static strength, fatigue strength and damage tolerance proposed by the design unit. This process is obviously difficult. More importantly, the civil aviation manufacturing industry has a stricter quality evaluation system than the aerospace, military aviation and other manufacturing fields, and a new process must be approved by the airworthiness authority.
With the launch of my country’s large passenger aircraft project, the dual laser beam bilateral synchronous welding technology for the T-shaped connection structure of the fuselage panel skin stringer has been studied in China, and preliminary results have been achieved. However, at present, the mature technology of double laser beam double-side welding of fuselage panel skin, long truss T-shaped structure has not been mastered in China, and it is still difficult to produce the overall welded panel of the fuselage of large passenger aircraft that meets the requirements.
The Technological Analysis Of Laser Welding Of Large Passenger Aircraft Fuselage Panels
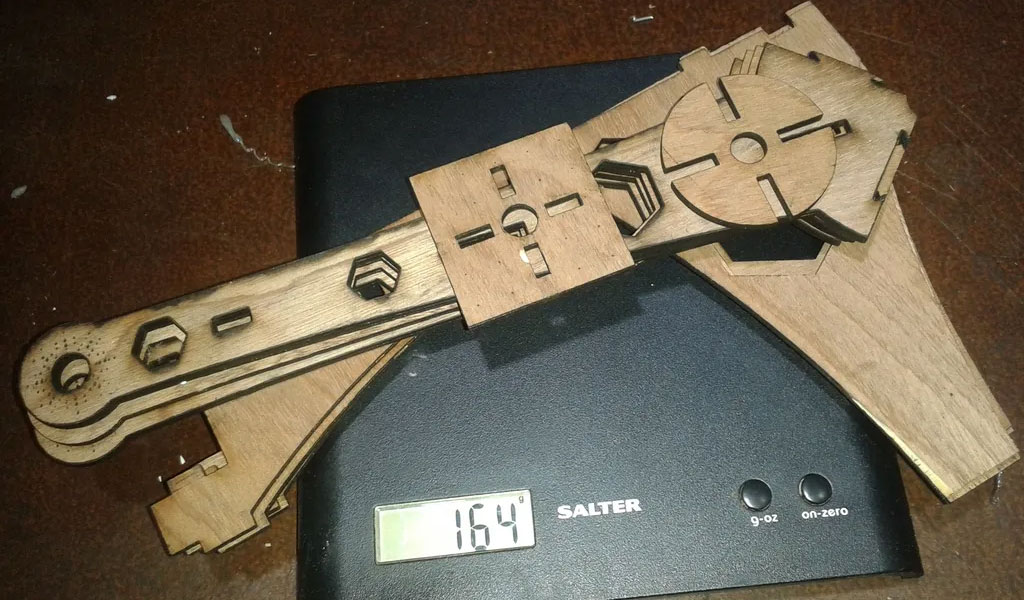
1 Welding Process Stability
In the laser-welded components of the long truss skin of the fuselage panel of a large passenger aircraft (Figure 3), the length of a single weld may be more than 4m. At the same time, since the skin and the truss are very thin, can the stability of the welding process be effectively maintained? It is one of the keys to the success of welding production. In this scheme, dual laser beams are used for simultaneous welding on both sides of the inner side of the skin. In order to maintain the integrity of the outer side of the skin, the welding process cannot penetrate the skin, and the T-shaped structure does not need to emphasize the aspect ratio too much. Forming a continuous, defect-free, high-performance welded joint is the key. Therefore, it is necessary to maintain the stability of the small holes and molten pools in the laser deep penetration welding process. It is mainly considered from two aspects: on the one hand, from the perspective of welding tooling and equipment support, it is necessary to maintain high-precision clamping and laser focusing and centering, and keep the robot (or CNC machining tool) controlling the welding head movement process. Repeat positioning accuracy and trajectory positioning accuracy, if necessary, use an appropriate tracking system; on the other hand, due to the good fluidity of liquid aluminum alloy, low surface tension, poor stability of the molten pool, and at the same time, the ionization energy of aluminum element is low, during the welding process Photoplasma is prone to overheating and expansion, which also leads to poor welding stability, so it should be studied from the perspective of welding metallurgy.
2 Welding Defect Control
Defects formed in the welding process are the most important factors that directly affect the welding quality. For the aluminum alloy laser welding process of large passenger aircraft wall panels, the most likely defects are pores and cracks.
Regarding the formation mechanism of porosity in aluminum alloy laser welding (Figure 4), there is still no unified and complete theory, and it is generally believed that there are two factors, metallurgy and technology. At present, there are mainly the following views:
- During the cooling process of the molten pool, the solubility of hydrogen drops sharply to form hydrogen pores;
- The evaporation of alloy elements with low melting point and high vapor pressure causes pores;
- The metal fluctuation of the molten pool, the turbulent flow of the molten metal and even the instability of the small hole lead to the formation of pores;
- Poor fluidity of the molten pool is also a factor leading to the formation of pores.
In a word, it is necessary to carry out research on specific materials and specific welding structures to find the formation mechanism of pores, so as to study the method of controlling pores. According to the research that has been carried out at home and abroad, the porosity of aluminum alloy laser welding is a problem worthy of attention, but it can generally be solved through metallurgical analysis and process optimization.
The fusion welding process of aluminum alloys is generally sensitive to hot cracks, and the hot cracks are mainly crystalline cracks. The research shows that in the later stage of crystallization of the weld pool, the cracking of the low melting point eutectic at the grain boundary under the condition of tensile stress is the main way for crystallization cracks to appear. Since aluminum alloys are typical eutectic alloys, crystallization cracks are more likely to occur. For laser welding of aluminum alloys, the welding speed is high, and the excessively fast cooling rate leads to high thermal stress, high stress gradient and crack re-expansion, which are also factors that promote the formation of crystalline cracks. The main measure to prevent thermal cracks is to use filler materials during laser welding. The mechanism is to make the alloy composition of the molten pool avoid the maximum solidification temperature range as much as possible, to refine the grains by adding nucleating agents, and to increase the flow of liquid metal in the molten pool. sex, etc. In addition, adjustments can be made from optimizing welding process parameters, such as using a small heat input to reduce the overheating zone, and using a relatively small welding speed to reduce the strain rate.
In addition, welding defect control is closely related to process stability. For example, the instability of the welding process causes the welding pool to vibrate violently, and defects such as undercut and discontinuous welding seam formation are prone to occur. For the laser welding process of long truss structure of large passenger aircraft fuselage panel skin, the beam quality of dual laser beams is one of the important factors that determine the stability of the welding process and the formation of defects. Not only the two laser beams are required to have high beam quality, but also the two laser beams are required to be strictly symmetrical. For this reason, the two laser beams on both sides of the skin truss T-shaped structure should come from two identical laser generators, or the laser beams generated by the same laser generator should be split into two identical laser beams.
3 Non-Destructive Testing Technology And Evaluation Criteria For Welding Defects
The welding process will inevitably produce defects, and the aircraft component products cannot be zero-defect requirements. As long as the specification standards established according to the design requirements are met, and the tests and production are carried out according to the relevant specification standards, the welded components can bear the load conditions during the service life. Due to the particularity of civil aviation products, it is impossible for aircraft welded components to be tested by sampling and to use destructive testing techniques to detect welding defects. Usually, non-destructive testing is required for aircraft welded components. Due to the short application history of laser welding in the aviation field, there is currently no standard for laser welding non-destructive testing and defect evaluation indicators in the relevant standards. Therefore, it is an important part of the laser welding process research of large passenger aircraft to carry out research on nondestructive testing technology of welding defects and formulate reasonable process specifications.
For large passenger aircraft skin truss laser welding structure, due to the large size and thin thickness of the skin, and the special welding structure, the use of traditional ultrasonic, X-ray and other technologies has its own limitations. In addition, the evaluation of traditional X-ray inspection film negatives relies too much on the technical level and proficiency of workers, and the automatic identification and evaluation technology of new digital negatives is not mature enough at present, and there is no standard to follow. To this end, it is necessary to extensively examine the successful experience in related fields at home and abroad, study the non-destructive testing technology and equipment suitable for welded components of large passenger aircraft fuselage panels, and formulate a reasonable evaluation standard system for welding defects.
4 Welding Deformation Control Technology
Compared with the traditional riveted fuselage panel, the laser welded fuselage panel has obvious weight reduction effect, which can improve the performance of the connection part, and at the same time, it has the advantages of reducing the manufacturing cost and improving the production efficiency. However, the stress concentration and deformation problems caused by laser welding do not exist in the riveting process. The laser welding process of large passenger aircraft fuselage panels is a complex welding process with large size, small thickness and multiple welds, and its deformation process is very complicated. Figure 5 shows the simulation results of welding deformation of a typical panel piece, which is the result of a thermal-mechanical coupling analysis for a typical panel panel (3 stringers) of a large passenger aircraft. As shown in Figure 5, even if the preferred center-symmetric welding technology is used (the welding direction is the same, the order is the middle and the two sides), there is still a large amount of deformation. Experimental studies have also shown that for multi-stringer members, the deformation mechanism is complex.
The research of laser welding deformation control technology can adopt the method of combining finite element simulation with deformation control and orthopedic technology. First, the finite element simulation technology can be used to predict the welding stress and deformation under different process conditions, and to study the welding deformation law of large passenger aircraft panel components, so as to optimize the ideal welding process parameters. Then, carry out research on deformation control and orthopedic technology before welding, welding process and after welding, such as jet impact heat sink treatment, welding rolling technology and shot peening orthopedic technology, and finally form the deformation control of large passenger aircraft fuselage wall panels by laser welding Technology System.
Concluding Remarks
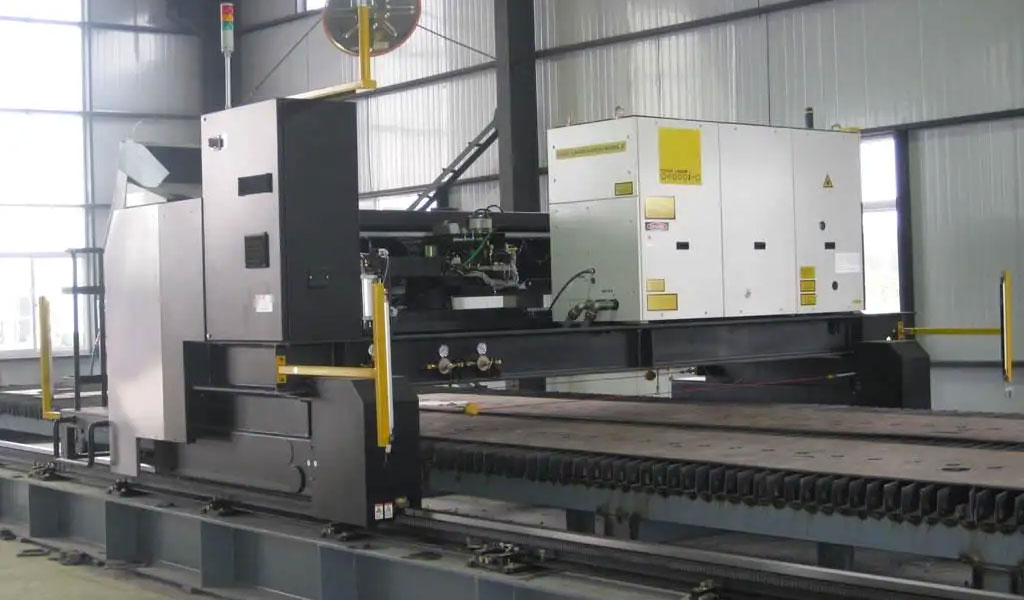
In the long run, the welding technology in the production of large passenger aircraft must conform to the characteristics of the aviation manufacturing industry and the development direction of digitization, informatization, intelligence and flexibility of the contemporary manufacturing industry. It is necessary to carry out research on digital modeling and finite element simulation of welding process, develop welding expert system for welding parts of large passenger aircraft, and realize digital welding information sharing and process control.
Large passenger aircraft laser welding process research is a technical system that integrates welding metallurgy, welding structure design, welding process control, non-destructive testing of welding defects, welding simulation simulation and even digital welding. Due to the particularity of civil aircraft products, there are still many technical difficulties to be overcome in the laser welding technology system of large passenger aircraft. Today, with the rapid development of laser welding, in view of the successful application of foreign advanced aviation manufacturing enterprises in large passenger aircraft, based on the long-term achievements of the majority of welding researchers in my country in the field of aluminum alloy laser welding, such as COMAC and related participating units in The fruitful results have been achieved in this project, and it is believed that the laser welding fuselage panel manufacturing technology in the production of large passenger aircraft in my country will soon be realized.