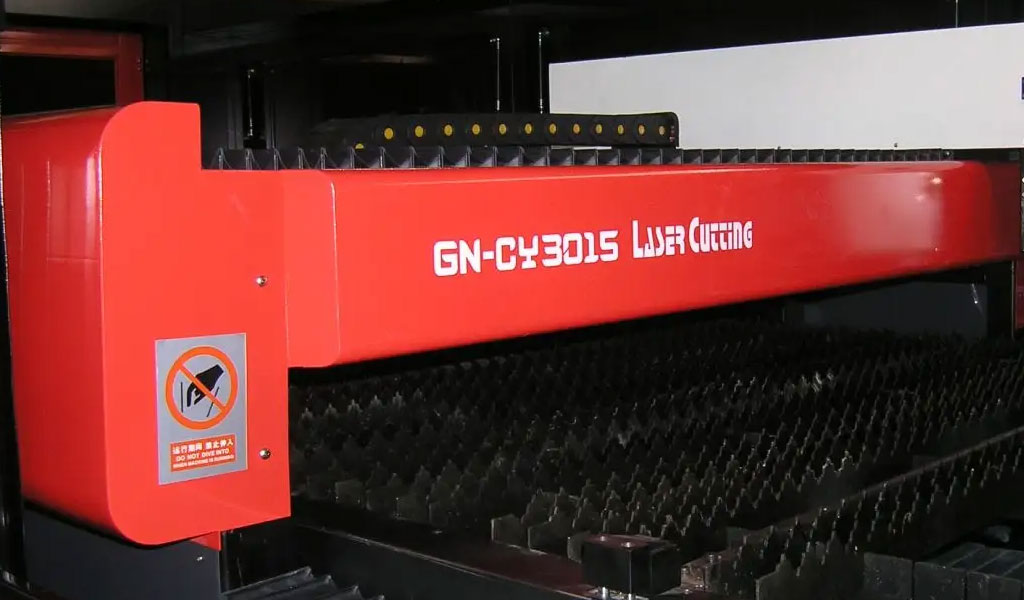
With the continuous development trend of the sheet metal fabrication industry, the market competition in this industry will gradually become fierce in the future. Due to the different sheet metal processes, fabrication equipment and customer requirements, there are very different types of sheet metal fabrication, as follows.Types of sheet metal fabrication.
1、Water Jet Cutting
Another sheet metal cutting method is water jet cutting. Water jet cutting uses extremely high pressure water jets (which can also be mixed with abrasives) to form a kerf in the material. It is a superior manufacturing method to laser cutting when cutting low melting point materials such as plastics and aluminium, preventing unwanted distortion.
2. Plasma cutting
The third and most powerful method of cutting sheet metal is plasma cutting. Plasma cutting works by generating an electrical channel of extremely hot ionising gas (plasma) which melts the material to create the cut. It is an effective method for cutting materials over 10 mm thick, but the cutting accuracy is not the same as laser or water jet cutting.
3. Laser cutting
One of the key methods for cutting sheet metal is the use of a laser cutter. Laser cutting uses a high energy beam enhanced by a lens or mirror to burn/vaporise the material to create the cut. This is a very fast and accurate method of cutting sheet metal and the potential for warpage is reduced as there is less heat affected zone. CO2 and fibre lasers are most commonly used and can cut material up to 10mm thick.
4. Guillotine
The sheet metal guillotine is an effective method of creating clean, accurate cuts in sheet metal. The sheet is fed between two blades, which are then strongly compressed together to deform the sheet until the final cut is produced. The guillotine is a quick and inexpensive method of producing a high quality cut, although it does deform the metal edges slightly.
5. Stamping
Sheet metal stamping uses a similar cutting mechanism to the guillotine, however, it uses a formed metal tool (called a die) to make the cut. The die is forced into the sheet metal at high speed to perforate the sheet metal. Dies of standard shapes (round, square, rectangular) are usually used, however, bespoke tools can be made to punch more complex shapes. Due to the cost of making the tooling, this method is more suitable for high volume production.
6. Bending
Bending is the basic manufacturing process for forming sheet metal into functional parts. Sheet metal is bent using a machine called a bending machine, which consists of an upper tool (punch) and a lower tool (V-die). The material is placed between the tools and the punch is pressed downwards into the V-die to form the bend. The bending angle is determined by the depth of the punch pressed down into the V-die.
7. Assembly
Cutting and bending are the two ways of forming sheet metal, assembly is the third. Sheet metal parts can be assembled using mechanical fasteners such as bolts, screws and rivets. Or they can be joined using a welding process, where two or more parts are fused together using high temperatures and then cooled to form a joint.
This is all we have to share about what types of sheet metal working are available. In addition, we should also pay attention to choosing quality materials to play a practical role. This is also an aspect of sheet metal fabrication that needs attention.