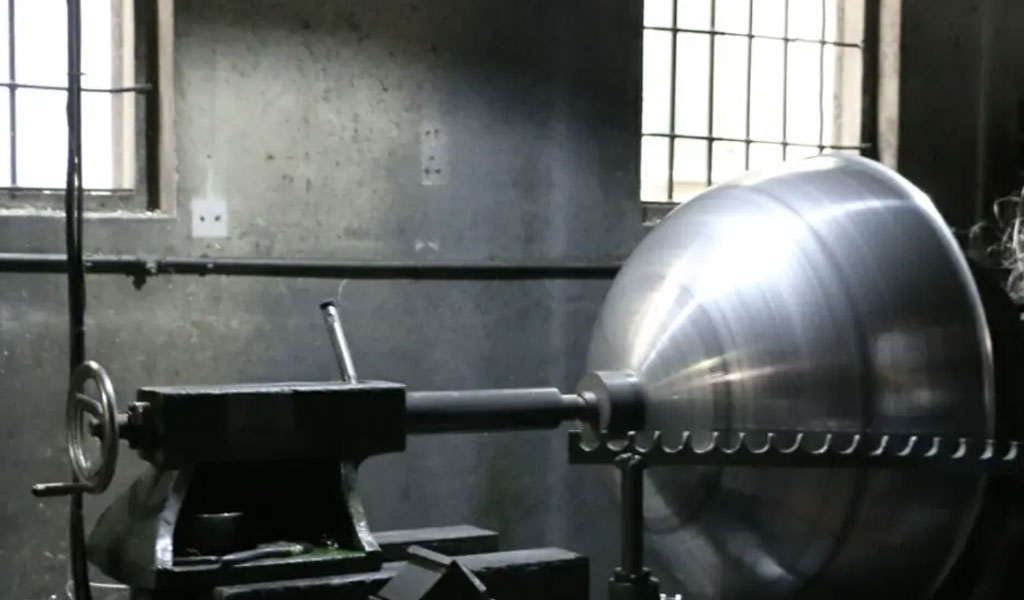
Spinning technology, also known as metal spinning technology, is a technology that rotates the force point from point to line and from line to surface, and at the same time applies a certain pressure in a certain direction to deform and flow the metal material along this direction to form a certain shape. Here, the metal material must have plastic deformation or flow properties. Spinning is not equivalent to plastic deformation. It is a complex process that combines plastic deformation and flow deformation. It is particularly important to point out that the spinning technology we are talking about is not a single strong metal spinning and ordinary spinning, but a combination of the two; strong spinning is used for the processing technology of spinning shells of various cylinders and cones. It is an older and more mature method and process, also called rolling method.
Basic principle Of Metal CNC Spinning
The basic principle of metal spinning technology is similar to the ancient pottery production technology. Spinning parts are generally rotating cylindrical parts or disc-shaped parts, and the spinning blanks are usually thick-walled cylindrical parts or round sheets. The principle and structure of the spinning machine are similar to those of a metal cutting lathe. At the position of the lathe’s large slide, a rotating wheel frame with axial motion power is designed, and the rotating wheel fixed on the rotating wheel frame can move radially; a core mold (shaft) is coaxially connected to the main shaft, and the spinning blank is sleeved on the core mold (shaft); the rotating wheel is passively rotated in the opposite direction by the friction generated by the contact with the blank sleeved on the core mold (shaft); at the same time, the rotating wheel frame moves axially under the action of the axial large thrust cylinder. Under the joint action of the axial force of the rotating wheel frame and the radial force of the rotating wheel, the surface of the blank is continuously plastically deformed point by point. At the position of the tail top bracket of the lathe, a tail top hydraulic cylinder with the same axis as the main shaft is designed, and the hydraulic cylinder applies axial thrust to the end face of the blank sleeved on the core mold (shaft).
Technical process Of Metal CNC Spinning
There are two types of spinning: ordinary spinning and strong spinning. Spinning that does not change the thickness of the blank but only changes the shape of the blank is called ordinary spinning; spinning that changes the thickness of the blank and the shape of the blank is called strong spinning. The spinning force required for strong spinning is relatively large, and the structure of the spinning machine is generally more complex. Strong spinning is divided into positive spinning and reverse spinning according to the direction of the spinning wheel movement and the direction of metal flow. The direction of the spinning wheel movement is the same as the direction of metal flow, which is called positive spinning; on the contrary, it is called reverse spinning. For the same material, the spinning force required for reverse spinning is relatively large. Which spinning method to use for forming should be determined according to the shape of the part and the process requirements.
The selection of the spinning machine is determined by the spinning process and various forming process conditions. Spinning machines are divided into two types: strong spinning machines and ordinary spinning machines. Strong spinning machines are divided into double spinning wheels and three spinning wheels. There are also spinning machines for special parts spinning, such as hot spinning machines, steel ball spinning machines, etc.
In mechanical products, how to save raw materials while improving product quality, reduce product weight while extending service life, and reduce product manufacturing costs and energy consumption while reducing processing hours has always been a concern for people. For example, “V” pulleys (commonly known as “V” pulleys) are one of the most widely used mechanical transmission parts. If they can be formed from steel plates, it is of great significance. Compared with traditional cast iron pulleys, sheet pulleys can save more than 70% of raw materials. Sheet-made spun pulleys formed by stretching and spinning metal sheets are the latest and best pulley structure. This pulley not only has the above advantages, but also has no environmental pollution, especially in a variety of mechanical products such as automobiles, tractors, harvesters, air compressors, etc. It is made by using steel sheet blanks on a special pulley spinning machine to make the blanks produce plastic deformation from point to line and from line to surface.
There are generally three basic forms of spun pulleys: folded pulleys, split pulleys and rolled multi-V pulleys (also called multi-ribbed pulleys).
Compared with cast iron pulleys, the advantages of spun pulleys are that they are made by spinning technology (chipless processing), light structure, and material saving, so the moment of inertia is small. It is a new product that saves materials and energy. High production efficiency (2 to 4 pieces per minute), good balance performance, generally no balancing treatment is required. Since the material flow line is not cut off, the surface is cold-worked and hardened, the tissue density is improved, the strength and hardness of the wheel groove surface are improved, and the dimensional accuracy is high, the slip difference between the V-belt and the wheel groove is small, and the belt life is long.
Development History Of Metal CNC Spinning
The development history of metal spinning technology in my country is nearly 40 years, and its application research in the defense industry is particularly extensive, and the research and application level is very high, especially in the spinning forming process and equipment, which has been in a leading position in China. The design and manufacturing capabilities of the spinning machine are also very strong. The pulley spinning process and equipment are an advanced technology. The pulley spinning process has achieved a series of scientific research results in folding pulleys, split pulleys, rolling multi-V pulleys and combined pulleys. Various technical problems in spinning forming have been solved in both theory and practice, and have been successfully used in production. However, compared with Germany’s spinning technology, my country still needs to work hard to catch up, because many of our products still need to be imported, especially some parts in automobiles.
Spinning Products
CDC-S series CNC spinning machines are special equipment for producing spinning pulleys. As a new process product, spinning pulleys have been widely used in automobile engines, such as motor wheels, water pump wheels, power steering pump wheels, air conditioning wheels and fan wheels. According to the groove type and processing technology of the pulley, it can be divided into three categories: split wheels, folding wheels and multi-wedge wheels. Due to the different structural characteristics of these three types of spinning pulleys, their processing technology is also different.
The material thickness selected for the multi-wedge wheel is 2-6mm, generally 3mm. The blank is made by deep drawing and stamping, and processed on the spinning machine. Since the tooth shape is formed by extruding the material wall thickness to produce metal flow and plastic deformation, there are many factors that affect the final quality of the product, including upper and lower molds, spinning wheels, process parameters, material materials, etc. It will be introduced in detail in the subsequent process analysis and mold design.
The material thickness selected for the folding wheel is 1.5-2.5mm, and it is also made by deep drawing and stamping, and processed on the spinning machine. Since there is no metal flow during the forming process of the folding wheel, the process is relatively simple and there are not many factors that affect the quality.
The material thickness of the split wheel is generally 4mm. Generally, it is made by one-time punching. The material is split from half of the thickness on the spinning machine with a titanium spinning wheel and then shaped. Since its processing technology is also relatively simple, there are not many factors that affect the quality. The most important factor is the flatness of the blank itself. Therefore, the requirements for the punching die are relatively high.